Digital twin technology is rapidly transforming the manufacturing industry, ushering in a new era of efficiency, innovation, and precision. This cutting-edge technology creates a virtual replica of a physical object or system, enabling manufacturers to simulate, analyze, and optimize processes in real-time. In this blog, we will explore the applications, benefits, and future trends of digital twin technology in manufacturing.
What is Digital Twin Technology?
A digital twin is a dynamic, digital representation of a physical asset, process, or system that spans its lifecycle, from design and production to operation and maintenance. It integrates data from various sources, including sensors, IoT devices, and historical records, to provide a comprehensive, real-time view of the physical entity. By leveraging advanced analytics, machine learning, and simulation techniques, digital twins enable manufacturers to make informed decisions, predict outcomes, and optimize performance.
Applications of Digital Twin Technology in Manufacturing
- Product Design and Development
Digital twins facilitate enhanced product design and development by allowing engineers to create and test virtual prototypes. This reduces the need for physical prototypes, accelerates the design process, and minimizes costs. Engineers can experiment with different materials, designs, and configurations, ensuring the final product meets desired specifications and performance criteria.
- Predictive Maintenance
By continuously monitoring the condition and performance of equipment, digital twins enable predictive maintenance. Manufacturers can identify potential issues before they escalate into costly breakdowns, scheduling maintenance activities based on actual equipment condition rather than fixed intervals. This approach maximizes equipment uptime, extends asset lifespan, and reduces maintenance costs.
- Production Optimization
Digital twins provide real-time insights into production processes, enabling manufacturers to identify bottlenecks, optimize workflows, and enhance overall efficiency. By simulating different scenarios, manufacturers can determine the best strategies for production scheduling, resource allocation, and quality control. This results in improved productivity, reduced waste, and higher product quality.
- Supply Chain Management
Digital twins enhance supply chain visibility and resilience by providing real-time data on inventory levels, demand fluctuations, and logistics. Manufacturers can use this information to optimize inventory management, streamline operations, and mitigate risks. Digital twins also enable better collaboration with suppliers and partners, ensuring a more agile and responsive supply chain.
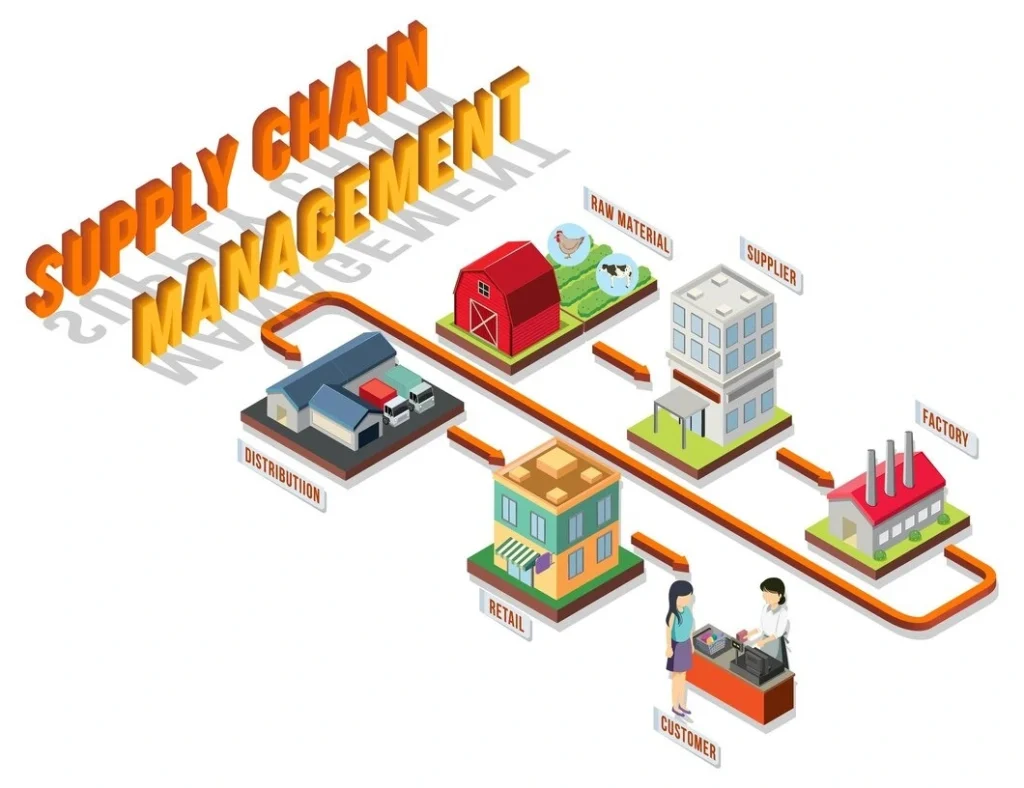
- Worker Safety and Training
Digital twins can simulate hazardous scenarios, allowing manufacturers to develop and test safety protocols without endangering workers. Additionally, digital twins can be used for virtual training programs, providing workers with hands-on experience in a safe, controlled environment. This improves worker safety, reduces training costs, and enhances skill development.
Benefits of Digital Twin Technology in Manufacturing
- Increased Efficiency
By providing real-time insights and predictive analytics, digital twins enable manufacturers to optimize processes, reduce downtime, and enhance productivity. This results in significant cost savings and improved operational efficiency.
- Improved Product Quality
Digital twins allow for continuous monitoring and analysis of production processes, ensuring that products meet the highest quality standards. By identifying and addressing issues early, manufacturers can reduce defects and enhance customer satisfaction.
- Enhanced Innovation
Digital twins facilitate rapid experimentation and iteration, enabling manufacturers to innovate faster. By simulating different designs and processes, manufacturers can explore new ideas and bring innovative products to market more quickly.
- Cost Savings
Digital twins reduce the need for physical prototypes, minimize maintenance costs, and optimize resource utilization. These cost-saving benefits enable manufacturers to allocate resources more effectively and invest in strategic initiatives.
- Sustainability
Digital twins help manufacturers reduce waste, optimize energy consumption, and improve resource efficiency. By minimizing the environmental impact of manufacturing processes, digital twins contribute to sustainable production practices.
Future Trends in Digital Twin Technology
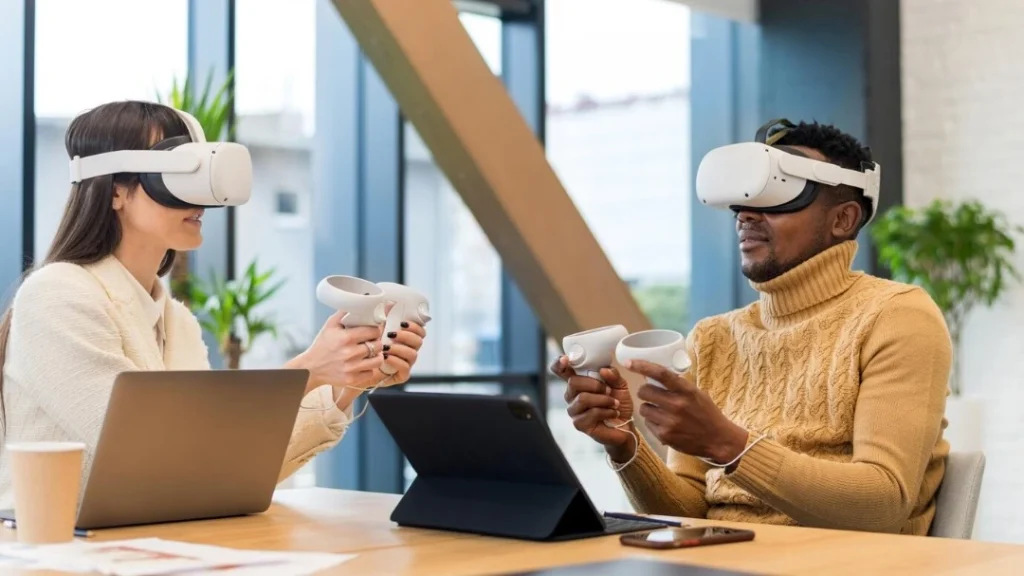
- Integration with Artificial Intelligence (AI)
The integration of AI with digital twin technology will further enhance its capabilities. AI-driven analytics and machine learning algorithms will provide deeper insights, enabling manufacturers to predict outcomes more accurately and make smarter decisions.
- Expansion to New Industries
While digital twin technology is currently most prevalent in manufacturing, it is expected to expand to other industries, such as healthcare, construction, and energy. The versatility of digital twins will drive innovation and efficiency across various sectors.
- Real-Time Collaboration
Advancements in digital twin technology will enable real-time collaboration among stakeholders, including designers, engineers, operators, and suppliers. This collaborative approach will streamline processes, improve communication, and accelerate problem-solving.
- Enhanced Cybersecurity
As digital twins become more integrated with IoT devices and cloud platforms, ensuring cybersecurity will be paramount. Future developments will focus on enhancing the security of digital twin systems to protect sensitive data and prevent cyber threats.
- Augmented Reality (AR) and Virtual Reality (VR) Integration
The integration of AR and VR with digital twin technology will provide immersive experiences for training, maintenance, and design. Workers will be able to interact with digital twins in a virtual environment, enhancing their understanding and decision-making capabilities.
Conclusion
Digital twin technology is revolutionizing the manufacturing industry, offering unprecedented opportunities for optimization, innovation, and efficiency. As this technology continues to evolve, manufacturers must embrace digital twins to stay competitive in a rapidly changing landscape. By leveraging the power of digital twins, manufacturers can drive growth, enhance product quality, and achieve sustainable production practices. The future of manufacturing is digital, and digital twins are at the forefront of this transformation.
Our Website Pricing Packages
-
Essential
-
$300.
-
Customized One-PageWebsite
-
Mobile Responsive Design
-
Basic (Up to 5 Pages)Content Creation
-
Contact Form Integration
-
Maintenance & Support
-
BasicSEO Optimization
-
Hosting Setup
-
Domain Registration Assistance
-
Blog Setup
-
Social Media Integration
-
Google Analytics Integration
-
Payment Gateway Integration
-
Product Catalog Setup
-
Business
-
$672.
-
Multi-Page (Up to 10 Pages)Website
-
Mobile Responsive Design
-
(Up to 10 Pages)Content Creation
-
Contact Form Integration
-
Maintenance & Support
-
SEO Optimization
-
Hosting Setup
-
Domain Registration Assistance
-
Blog Setup
-
Social Media Integration
-
.Google Analytics Integration
-
Payment Gateway Integration
-
Product Catalog Setup
-
E-Commerce
-
$1345.
-
E-CommerceWebsite
-
Mobile Responsive Design
-
(Up to 15 pages)Content Creation
-
Contact Form Integration
-
Maintenance & Support
-
.SEO Optimization
-
Hosting Setup
-
Domain Registration Assistance
-
Blog Setup
-
Social Media Integration
-
E-Commerce Tracking &Google Analytics Integration
-
Payment Gateway Integration
-
(Up to 50 Products)Product Catalog Setup